-
Service & Technical
- BD & Tradewinds 12/24 VDC
- Baitfreezer 110/220 VAC
- BG 1000 110/220 VAC
- BG 2000 110/220 VAC
- Cool Fish RSW Chiller
- DC 5000 12/24 VDC
- Engine Drive Refrigeration
- Engine Drive Air
- Shore Assist 110/220 VAC
- Our Products
- Price List
- Miscellaneous
Keel Cooler Test
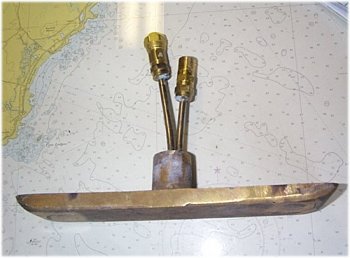
The job of this component in a refrigeration system is to cool the refrigerant as much as possible.
We made a bronze casting 10" by 2 3/8" by ½." This is larger than any keel cooler on the market. The radiating surface is 28 square inches.
The keel cooler was floated on a piece of foam in a 20 gallon barrel of 70 degree F. water. Water was circulated with a pump creating a surface flow around the cooler maintaining a constant water temperature.
Observations
After several minutes of BD compressor operation (at maximum capacity) the refrigerant discharge temperature/pressure rose excessively to more than 30 degrees F. higher than normal operating temperatures for an air-cooled compressor in 70 degree F. air. This is more than 55 F. degrees above water temperature. This temperature was even higher with the circulating tank pump off. With still tank water at 70 F., refrigerant temperature/pressure was over 60 degrees above the water temperature. Layers of still water around the keel cooler insulate and reduce the transfer of heat to the water. The stirring motion of water around this keel cooler is an improvement, giving lower temperatures, but this keel cooler is no match for the other condensers.
What is Efficient
As an example, efficient water-cooled condensers operate at 15 degrees F. above water temperature. Air condensers operate at 25 degrees F. above air temperature.
The chart below plots the operating pressures of identical systems being cooled four ways. One test with the keel cooler in still water, then the water being moved around the keel cooler with a pump, the comparison for this test is forced air cooling and a system with water cooling using a pump and counter flow condenser.
It should be noted that at all water temperatures the compressor is working harder with the keel cooler in comparison to air-cooling with the same or higher air temperature.
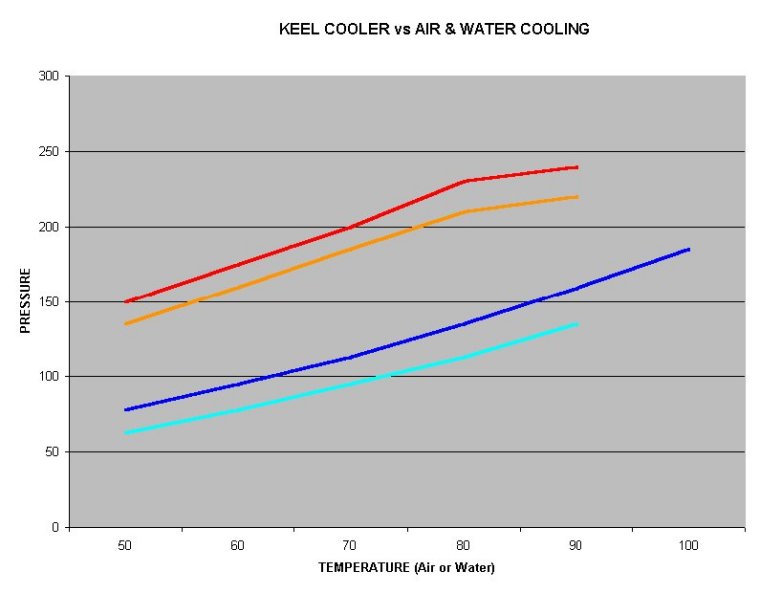
Legend:
- Top line: (red) Keel cooler in still water.
- Second line: (orange) Keel cooler in moving water.
- Third line: (dark blue) Ducted air cooling.
- Bottom line: (light blue) Counter flow water condenser with pump.
Note: This chart shows the pressure of the refrigerant. Pressure must be converted to temperature at each test point using an R-134a pressure temperature chart in order to make temperature comparisons.
High Temperatures Rob Efficiency
Compressor efficiency (BTU's per WATT) drops when the high pressure/temperature created by poor condenser cooling increases the compressor amp draw and compressor shell heat. Temperature and pressure are related, high temperature makes high pressure. The more pressure the compressor has to produce the more energy (watts) it will require to operate.
In this test the electronic compressor control module was not being cooled other than by static airflow.
The promotional advantage of the keel cooler is to eliminate moving parts like pumps and fans. Danfoss, the compressor manufacturer, requests fan cooling of the compressor and electronics when operating at the compressor's maximum capacity. Maximum capacity is needed in tropical operation in all but the smallest cabinets. For component life, fan cooling the compressor with a keel-cooled installation is a must. Adding a fan will not improve keel cooler performance but will help protect the components from heat failure.
Why the Keel Cooler Fails
Excessively high temperatures develop in the keel cooler because the inlet and outlet are thermally connected in the same block of bronze. As they pass each other, the temperatures average, the outlet temperature of the condensed refrigerant rises well above the water temperature as it is reheated by the hot refrigerant coming into the keel cooler.
An improvement in this keel cooling design would be a long flat fin projecting from the hull. This would add surface area and reduce the layer of insulating stagnate water when the vessel is at rest. An inlet at one end and an outlet at the opposite end might separate the temperatures and achieve refrigerant cooling to the water temperature. At some point in a proper design this cooler becomes a large external metal object on the outside of a smooth hull.
Air-Cooled Condenser Efficiency
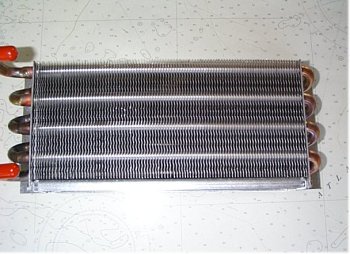
The Seafrost air condenser has 100 aluminum fins covering 80 inches of 3/8" copper tube. The total radiating area is 700 square inches (4.86 square feet) the inlet and outlet are separated so that the refrigerant exit temperature is at ambient air temperature. Air is forced through the condenser with a fan drawing 1/3 of an amp. The improved cooling of the components and the lower temperatures of forced air cooling make this method more efficient than a keel cooler. The compressor works less, installation is simpler, and there are fewer connections. Installation cost is lower and the system is totally servicable.
Water Cooled Condenser Efficiency
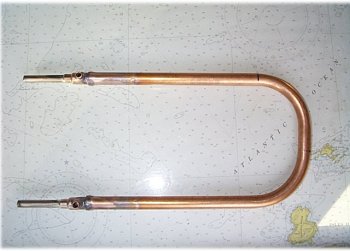
The Seafrost water cooled condenser is a 3/8"OD copper/nickel alloy tube jacketed with copper. Water flows in to the bottom of the copper/nickel tube pumped by a remote pump. Refrigerant flows in the top port and flows between the jacket and the copper/nickel tube, exiting at the bottom port near the water inlet. This counter flow of water against refrigerant allows the coldest refrigerant to meet the coldest water for cooling to water temperature.
Advantage of Forced Air-Cooling:
- An air condenser is scrubbed by air forced though it. This eliminates an insulating layer of air.
- Inlet and outlet of the air-cooled condenser are separated allowing maximum efficiency.
- The compressor and electronics are forced air cooled as required for full load operation. This extends the reliability and the system service life.
- Higher capacity can be obtained over a keel cooler.
Advantage of forced air-cooling with the addition of pumped water-cooling. All of the above plus:
- Water and refrigerant flow in opposite directions (counter flow design) through the condenser to cool refrigerant to water temperature.
- Flow of pumped water scrubs water and heat away for excellent thermal transfer.
- Maximum capacity can be extracted from the compressor.
Disadvantages of the keel cooler:
- Less energy efficient, poor heat rejection, runs hotter than fan cooling.
- Runs extremely hot when boat is at rest in still water and hotter still at rest and fouled with marine growth.
- Does not have a fan to cool electronics and compressor for recommended high output compressor use.
- Requires large hole in the hull.
- Creates drag. Reducing boat speed.
- May require zinc maintenance.
- Requires diving for cleaning. (anti-fouling)
- Potential electrolysis problem.
- Keel cooler must be remotely located under floorboards etc.
- Extra refrigerant connections in damp area below the water line are subject to corrosion.
- Extra tubing runs from the compressor to the keel cooler and back to refrigerated space.
- Cannot be operated on the hard. (Boat on land.)
- Requires haul out for replacement.